Jack talked to Giambattista Mele, sales manager at Elitron and Allan Ashman, managing director at Atech (the UK distributor), on the Elitron stand at FESPA to find out more.
Transcript of the video
Elitron at FESPA. We are exhibiting two systems, two cutting systems. The first, the bigger one, is our premium line named Kombo. That machine is a Kombo THC, and Kombo is our premium series of machines. It’s a double-edged machine with two independent heads with different tools on it, and it is able to cut all the materials that you can find in the visual communication market. So, you can find rigid or flexible materials, thick or very thin. The machine is a classic machine for the visual communication sector, but with a double edge, so you can have more flexibility and more productivity at the same time.
This version of the machine is also equipped with an addition: a feeder for managed corrugated material with printing on the bottom side. So the SDS, a special version of our visual system that is on the first part of the machine, is equipped with two cameras on the bottom side that can read the reference mark from the bottom. This means you can put the material on the table, and it can be cut without reading a barcode on the machine because the material has been prepared beforehand. Yes, so you can increase your productivity in this way, and you can cut and crease the material simultaneously and in a faster way. That’s the main feature of this kind of machine.
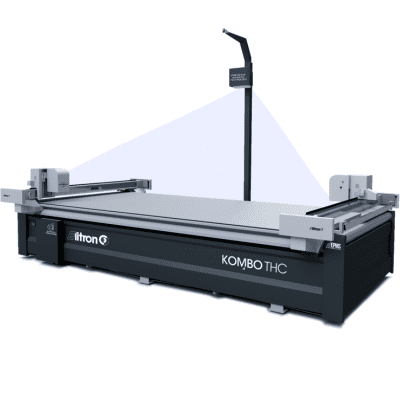
The same system can be equipped with a stacker system, which is not present here at Fespa for reasons of space, obviously. This can be different according to the different needs of the customer. You can have a standard conveyor belt table or a stacker with an elevator to put a pallet on and collect the single-cut pieces.
I think the most important words to use are flexibility and automation for us. I think that you can find a lot of automation at FESPA, and we can’t miss out on this. I mean flexibility and automation: less people, more production. So you can put work on this machine, walk away, it’ll finish it for you, and you can come back. So you’re not loading sheet by sheet; you’re loading a job. Yes, and FSDUs (free-standing display units), and even hoarding work and trays, because this machine is equipped with a router, so we can route ACM as well.
Yes, I think that we are receiving a good response from people for both the entry-level system, the Spark system. This is not new, but it’s a new version with new software for recognising both the single image printed on the material and the reference mark printed on it. It is an entry-level system; it is flexible, it’s cheaper than the premium series, it’s smaller, and it is a good solution for prototyping, sampling, and small production. And it is available with a fixed table or, like this one, with a conveyor one. So you can manage material in rolls in a very, very easy way.
So, it is a technology that we are importing from the leather sector. Generally, when you cut leather material, the leather skin is not regular in terms of perimeter and in terms of quality because you can find scratches, holes, and so on. So the operator that has to cut material must nest the single shapes to cut manually. This is important in the visual communication sector. Why? Because it is very, very easy to nest, very, very quickly, the shape to cut around the printed piece. And then you give information to the camera on the carriage of tools to read the marker, the reference mark, very fast. Otherwise, you would use the joystick on the machine to recognise the markers. Okay, so our operator sends the machine to read and centre quickly. So you can see on the screen there, the centring. This is an easy way to manage the work and the machine.
And then if you have, for example, some spare materials or very expensive material like acrylic, you can nest very, very quickly and cut without any further delay. And this is all available worldwide and in the UK.