Jack discusses the latest innovations in finishing machines from Plastgrommet at Fespa with Rafa Menendez, Sales and Marketing Director
PLASTGrommet at Fespa launched four new solutions for banner and textile finishing, including the All In One Edge entry-level finishing machine. Offering the same integrated welding, eyeleting, and cutting capabilities as the flagship All In One banner finishing machine, the All In One Edge is aimed at medium-sized companies at a fraction of the cost. The company will also launch new sewing automation capabilities for textile finishing with the TexWiz sewing module.
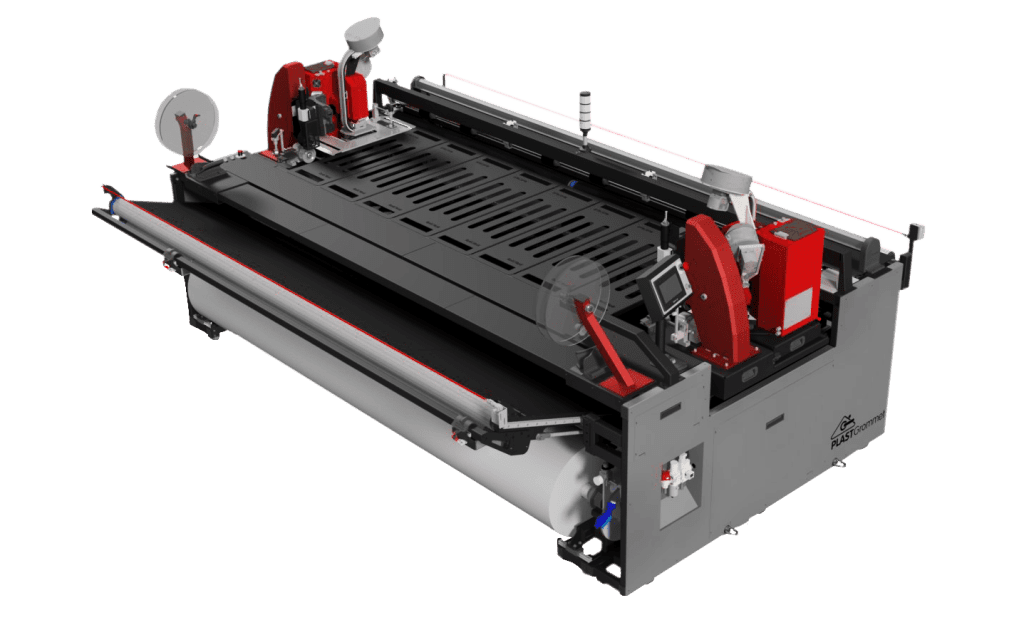
A neat addition to the range is the Winder360, designed to automatically rewind banners from the All In One, creating an efficient workflow. The fourth new solution on display is a new media roll lifter for Jumbo rolls in the form of the JumboMAX 1,000kg. Building on PLASTGrommet’s range of media roll lifters and media storage solutions, this new product enables large-format printers to easily move large rolls of media around the shop floor.
Transcript of Plastgrommet at Fespa video
Jack Gocher: So, here I am on the stand of Plastgrommet at Fespa with my old friend, Rafa Menendez. Hi, Rafa, nice to see you again.
Rafa Menendez: Nice to see you, Jack. As always.
Jack Gocher: Another year!
Rafa Menendez: Yeah, another year, here we are.
Jack Gocher: So, tell me, what’s new on the stand for Plastgrommet at Fespa this year?
Rafa Menendez: This year, we’re bringing a new finishing machine that has all the advantages of automation. So, we’re automating welding, eyeleting, and cutting. We have a camera system – all the benefits that customers are looking for – but with a very compact footprint and great flexibility in terms of the sizes we can finish. We can finish any width from 60 centimetres up to 3.2 metres. And it’s also, you know, at a lower price point than the All-in-One machine that we’ve been manufacturing for eight years now. We believe this is the kind of unit that most customers will be looking for because, while automation is needed, not everyone wants to make a huge CAPEX investment.
Jack Gocher: This is part of a bigger solution, isn’t it? You have media partners, printing partners, big printers, sewing machines – and this is almost the final part of that process?
Rafa Menendez: Exactly. One thing some customers don’t realise is that you’re only as fast as your slowest point. And that often happens to be the finishing. So, if you invest in a printer that is, say, 30 percent faster than last year’s model, what are you going to do with all that banner material? You have to finish it one way or another. If you do it manually, you’re going to need hours, hundreds of hours.
So, we have a lot of customers who say, “Okay, I want to invest in automation,” and what we’re trying to do is offer a solution for almost everyone. Some people will need full automation, for which we have the big All-in-One machine in the back. That’s our premium machine – really, really fast. And then there’s the All-in-One Edge, for which we’ve had very positive feedback here at FESPA. It’s aimed at any medium-sized company that really wants to automate its processes in a very cost-efficient way.
Jack Gocher: So, could we talk about one or two of the new features on these new machines that make them a real value to end-users?
Rafa Menendez: Yeah, let’s go around the machine because this is where we feed the material. A couple of very important features we have are inline trimmers, so we can trim the excess material as we go. This is useful because some customers can’t print edge-to-edge, or others, if they’re using a 1.6-metre roll and want to make a 100-centimetre banner, they can print it within that width.
Another feature is we have an alignment device here. So, if the rolls aren’t perfectly straight, everything moves left to right automatically. As we unwind, we correct the position of the roll, which is very important.
Next, we come to the welders. Here, we’re making the hems by folding the material with hot air to create the weld. We have a camera system here that scans for eyelet and cut marks. After the camera, we have the automatic eyelet machines. Once we’ve made the weld and inserted the eyelets, there’s a cutting unit. We clamp the material, and then a cutter comes from underneath and cuts it.
Jack Gocher: So, this is all about automation – doing the job of many people, but accurately and consistently. This really is…
Rafa Menendez: Yeah, I mean, in the past, when people talked about automation, it was often about reducing employee costs. These days, it’s different. Many businesses say they simply don’t have enough staff. So, if we can have a machine that does all these processes, the few people they do have can focus on other tasks. It’s not about a machine replacing a human; it’s about efficiency and having equipment that guarantees you can deliver orders on time. That is the most important thing these days.
Jack Gocher: And when you’re producing hundreds and hundreds at a time, they have to be the same, of course.
Rafa Menendez: Exactly.
Jack Gocher: I can see we’ve also got the lovely collection of grommets here.
Rafa Menendez: Yes, for a couple of years now, we’ve been able to offer all our equipment with options for clear plastic eyelets – that’s our main background, our main business. And we also manufacture metal grommets for customers who, for one reason or another, prefer a metal option. So, we let them choose, really.
Jack Gocher: So, this is the mid-range machine. Is there anything else new on the stand?
Rafa Menendez: We have something very new. This, as I mentioned, is what we now call our premium version, as we have two distinct offerings. A really new development is that customers have been asking if it’s possible to produce fabric mesh banners in a fully automated way. So, we’ve introduced a sewing module on the machine.
Here at FESPA, we’re demonstrating it by doing banner welding for an hour, then we change the media, and an hour later, we’re doing automatic sewing. So, we’re making a hem, inserting a webbing tape, setting eyelets, and cutting – all fully automated. One of the key advantages is that, for a polyester banner, we use polyester tape and polyester thread. Our clear eyelets are also fully compatible for recycling with polyester. This means the entire banner can be recycled in the polyester waste stream, which is a game-changer because you don’t have to remove the eyelets.
Jack Gocher: Okay, so I see this one is called ‘All-in-One’, and that one is also ‘All-in-One’?
Rafa Menendez: That one is the ‘All-in-One Edge’, as we call it.
Jack Gocher: Okay. Are these capabilities always integrated, or can the machines be configured as separate units?
Rafa Menendez: No, the idea here is that we didn’t have enough space at FESPA to show a dedicated textile finishing machine, so we’re demonstrating a hybrid solution. The feedback from customers who already have this solution is often, “Okay, what’s the cost of this addition?” because it might make sense for them to install it and have a flexible solution that can handle both banners and textiles. The set-up time is only about 15 minutes when changing from banner material to fabric, so it’s quite quick.
Jack Gocher: It’s a fantastic design, isn’t it? The way the different parts come together.
Rafa Menendez: Yes, it’s modular. That’s very important for us, as it means we can assemble the machines as quickly as possible at the customer’s site. This allows us to spend more time on training rather than on machine construction. And that modularity has been a great advantage, for example, allowing us to integrate the sewing module like this.
Jack Gocher: Okay, so are these machines available now?
Rafa Menendez: Yes, absolutely. This technology is available now.
Jack Gocher: And what are people saying who are coming onto the stand? Are we going to see it run in a minute?
Rafa Menendez: They love it, they really do.
Jack Gocher: Good, good. Well, look, I’m sure the show is going well for you.
Rafa Menendez: Yes, yes, we’ve had a lot of visitors over the last two days, and this morning has been very good so far.
Jack Gocher: Excellent. Well, I’ll let you get on. I appreciate your time.
Rafa Menendez: Thank you for stopping by, Jack.
Jack Gocher: Thank you very much.